"The GIS portal is truly a digital transformation of our entire power production and management process. It has freed up our staff to focus [more] on critical assignments and less on sharing paper maps, out-of-date data, and lack of efficiency and effectiveness."
case study
KenGen's GIS Portal Drives Digital Transformation
Kenya Electricity Generating Company (KenGen) is one of the world's leaders in sustainable energy. It boasts that nearly 90 percent of its 1.8 gigawatt of power is supplied by clean energy. It is also a leader in innovation by building a geographic information system (GIS) portal and a spatial data store that transformed its generation business.
Challenge
The increase in production facilities has resulted in a rising challenge for KenGen. This increase, plus rapid development in renewable energy, created mounds of data, demanding a paradigm shift. Traditional data management practices proved inadequate.
At the same time, presenting a view of the company's plant performance to decision-makers became a time-consuming and error-prone process. Local staff handled bulk digital and paper information with little sharing. This led to duplicate data. In addition, responding to peak workloads took too long, frustrating support staff.
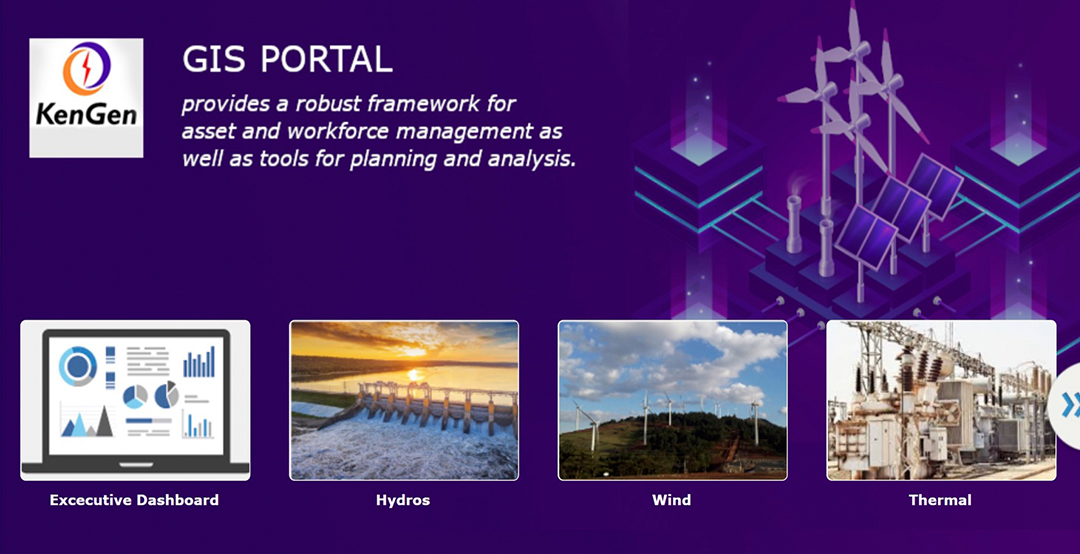
Solution
KenGen's geomatics team looked to innovation by striving for true digital transformation to meet these challenges. As a result, it created the GIS-based Integrated Resource Management Information System (IRMIS).
IRMIS lets KenGen decision-makers understand and track the status of assets and facilitate preventive maintenance at a glance. Assets include geothermal wells, buildings, power plants, and hydro dams. IRMIS can also manage power distribution at specific generation stations to prevent power supply disruptions. This innovation helps KenGen staff to know how and where their business stands from a geographic point of view. Managing this information based on location data required a well-designed framework that guided KenGen through a spatial transformation journey. This framework became a road map to the transformation success by embedding ArcGIS Enterprise to help KenGen staff meet the challenges they faced.
IRMIS features a GIS portal, which gathers digital data in one centralized place—the geodatabase. As a result, staff now access data about the performance of all the plants in near real time. IRMIS has seven major sections consisting of Executive Dashboard, Hydro, Wind, Thermal, Geothermal, Property, and KenGen Reports portals.
Queries on a single KenGen asset can be done effectively with just a click of a button, performing analytics and generating a report if need be.
Depending on the selections, users can navigate to specific plants or departments and select multiple data layers within each display, from small assets such as fire hydrants to major ones such as transmission lines. In addition, all the asset locations and their attributes are detailed. Further, KenGen integrated this information with the company's SAP plant management system.
Process
The geomatics team created the IRMIS by adopting the following steps:
- Identify spatial transformation objectives—The team determines the organization's
digitization level and aligns to the current state and long-term digital goals. - Formulate a transformation strategy—A feasible game plan is built by selecting improvement areas and integrating digital systems from those areas.
- Decide on the necessary technology enablers—Enablers, such as the Internet of Things (IoT), analytics, and the cloud, are conceived as vital drivers for a successful transformation.
- Establish a competent technology leadership and management—With robust management and leadership support, the shift has shown greater chances of success.
- Train the staff and integrate a digital culture among the staff members—As a result, the culture and education provided across the organization has made adapting to change easier, and each department embraces the shift.
"Geomatics serves various multidiscipline users. Before the IRMIS, spatial data sharing, maps, and reports were hectic and riddled with many calls from users. Not any longer. Since map data is available to all users at the click of a button through the IRMIS, efficiency is highly improved."
—Fred Wekesa, Head of Geomatics, KenGen
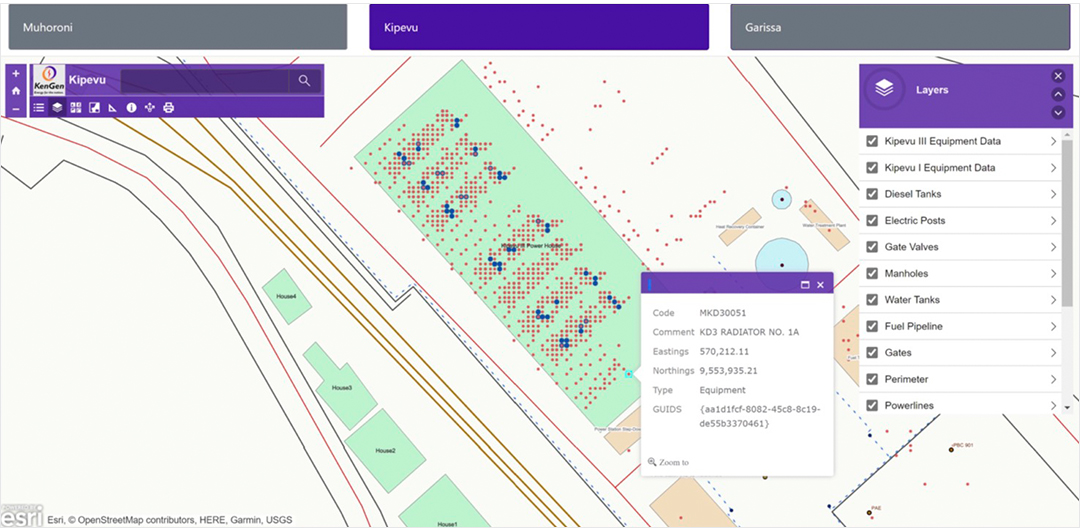
Partner
KenGen developed the system with the help of the local Esri distributor, Esri Eastern Africa. Esri Eastern Africa provided consultation, configuration, and training during the data model development, data migration, and app rollout to the users.
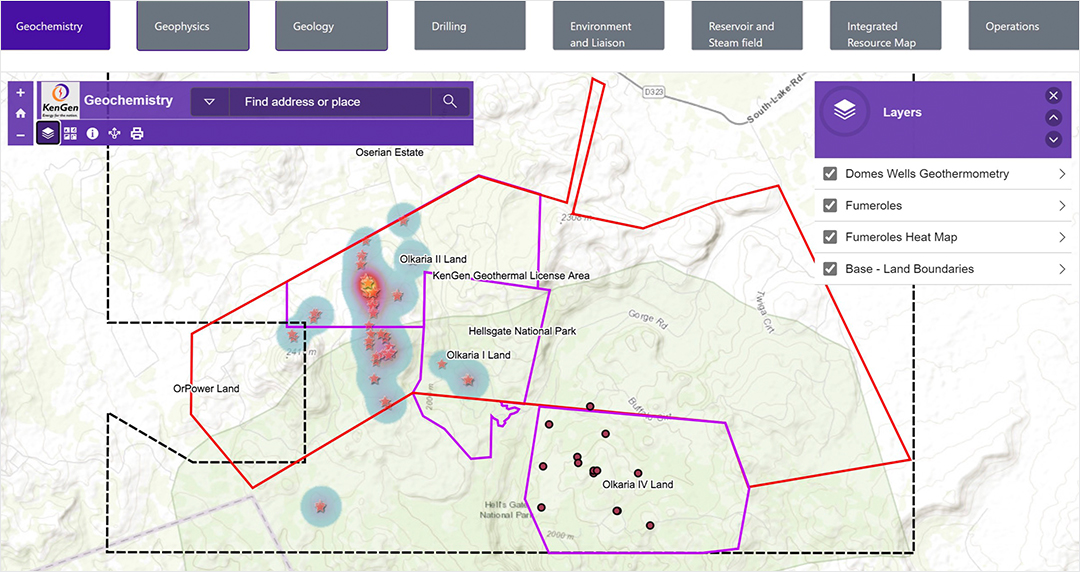
Results
The data consolidation proved so valuable that users began clamoring for maps of all kinds, creating a new problem. The 33 geomatic staff members became overwhelmed with requests from over 2,500 end users. So the team again innovated by adjusting the portal to be virtually self-service, allowing the users to pick and choose which maps and layers they needed.
KenGen houses and manages its spatial data in one place. This platform helps staff with problem-solving and, perhaps critical of all, collaboration and data integration. This innovation has eliminated duplicate and often inconsistent data and helped ensure a quick response. In addition, it includes an asset inventory.
The innovation yields many benefits, including cost savings, greater expertise, and custom module sharing. Gaps within the system are easily identified. Updating data has become easier due to frequent checks by an increased number of users, thus limiting operational errors. The transformation has presented a way to comprehend the complexity of KenGen by addressing and communicating the issues by using one common language.
IRMIS serves data for various uses, from engineering and design to project management. It serves new installations to operations and asset management, and it delivers data on all the properties and facilities for each power plant. In addition, it provides analytics on operations, allowing management to allocate resources and predict plant performance.
The portal allows users to create their own custom maps, increasing the usefulness of the portal while not overburdening the geomatics staff.
The system provides immediate access to critical data to its staff in all departments. Instead of users issuing requests for custom maps, they get the data they need more rapidly. Since the data is managed centrally, errors are quickly uncovered and fixed, providing a safer work environment. Managers can uncover issues faster, limiting production downtime. The benefits are many—cost savings; reduction of decision-making time; dramatic decrease in errors; a better safety environment; and overall improved plant output, limiting costly power purchases.
The dashboards provide a high view of the entire company's power generation performance. In addition, KenGen has leveraged the portal as a location to show the real-time operations of each plant, providing data from its plant SCADA systems. As a result, senior management can view operations at virtually any level of detail required. Greater insight has led to better and rapid decision-making.
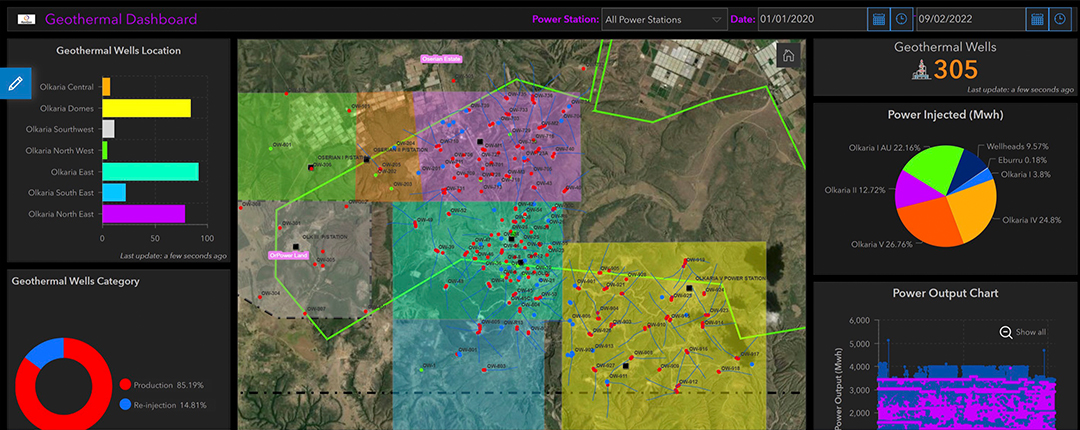
Next Steps and Emerging Trends
The system has proved to be extraordinarily popular. However, that popularity requires expansion. As a result, KenGen is looking to migrate to the cloud to provide increased performance and scalability. In addition, the company is planning to expand the self-service capability to its users, giving them the ability to create custom maps and analytics.
The system has proved to be so successful that KenGen has the attention of other power suppliers in the region. KenGen is actively working with other countries to implement the system, thus enhancing the efficiency of its neighbors' power plants.
Finally, KenGen plans to roll out drone-captured imagery, 3D representation of the assets, and the system as a critical component for its digital twin.
Want to know more?
Fill out the form below and someone will contact you regarding this case study