Argentina is among the top 30 crude oil producers in the world. The country’s Pan American Energy (PAE) Group is the leading private sector energy producer in the southern region of South America. It’s an integrated oil company that manages upstream, midstream, and downstream operations; generates electric energy; and is part of the renewable energy sector.
To achieve greater efficiency among its vast operations, leaders at the company decided to optimize PAE’s fuel delivery services. These go to retail petrol stations and other customers, such as airports that distribute jet fuel, located throughout the country.
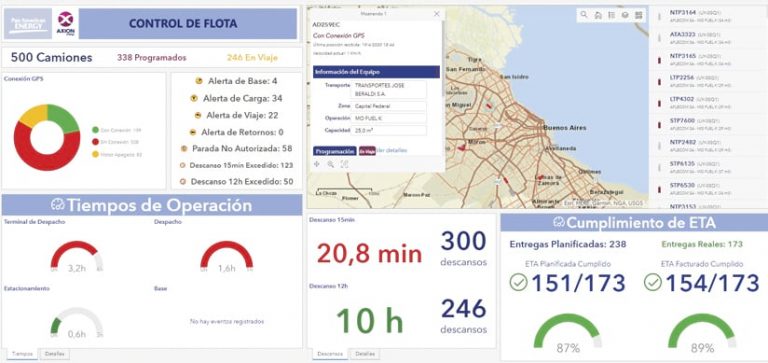
“Argentina is a large country with a varied terrain, so geography plays a big part in efficient fuel delivery,” said Gonzalo Fernandez Grossi, who served as senior IT project manager at PAE. “Since improving fuel delivery services is a geospatial problem, we decided to use our ArcGIS expertise to solve it.”
A Comprehensive Fuel Distribution Platform
PAE has used Esri technology for 15 years. So for this project, the company relied heavily on ArcGIS Enterprise and ArcGIS Online.
“We have more than 1,000 customers that are serviced by about 280 tanker trucks,” said Fernandez Grossi. “The fuel distribution to our customers is an outsourced service.”
For invoicing and distribution planning, PAE uses software from SAP and other complementary solutions. However, company leaders were concerned that they couldn’t monitor and control fuel distributions as they were happening. In addition, PAE was collecting very little transit information.
“The theoretical timeline that we originally created provided our customers with a five-hour delivery window, which was very difficult for them from a business perspective,” Fernandez Grossi explained. “So we decided to use Esri software—particularly ArcGIS GeoEvent Server—to resolve the lack of complete, accurate, and reliable information during the fuel distribution process. This helped us optimize costs and improve our customer relations and experience.”
PAE uses a comprehensive stack of Esri technology in its fuel distribution platform. ArcGIS Enterprise manages connections to PAE’s Oracle geodatabase and provides REST endpoints for published data and geoprocesses. The ArcGIS Enterprise portal is the content manager and the system’s security management node. This is because it integrates the Lightweight Directory Access Protocol, which is used for directory services authentication. The portal also hosts dashboards and apps that PAE’s IT team builds for end users. And ArcGIS Data Store provides an agile and stable repository for storing analysis.
The key to the system is GeoEvent Server, which ingests information—including truck positions, commercial master data, and scheduled deliveries—in real time. It analyzes events such as fuel drop-offs and driver rest stops based on business rules, generates alerts, and sends data to ArcGIS Enterprise or Data Store. GeoEvent Server also integrates with email and the WhatsApp messaging service to provide alerts via push notifications.
Another critical component of PAE’s new fuel distribution monitoring system is the Origin Destination (OD) Cost Matrix, a ready-to-use service from Esri that can be integrated into apps using ArcGIS REST APIs. The OD Cost Matrix is used to determine the least-cost paths in a transportation network from multiple origins to multiple destinations and to calculate estimated arrival times—in this case, for PAE’s fleet of tanker trucks. Additionally, the Node.js web server runs highly complex processes using the OD Cost Matrix to determine the particularities and logic of each trip. Node.js also synchronizes certain data from SAP endpoints (master data and delivery programming) and returns this information to GeoEvent Server for further analysis.
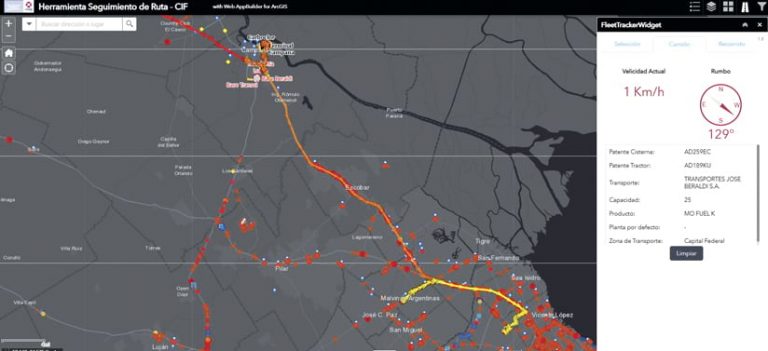
“The system we have developed provides us with complete, accurate, and reliable information during the fuel transportation process and quickly identifies deviations in the transport, allowing us to take corrective actions when necessary,” said Fernandez Grossi.
PAE Gets More Control, and Customers Get Better Service
PAE’s new fuel distribution monitoring system has proved very effective in optimizing its vehicle routing network. It enables staff at the company to oversee the daily distribution of fuels, lubricants, chemicals, and biofuels that are scheduled in SAP. It also allows them to check on the availability of hired trucks, monitor how long it takes to load and unload fuel, keep track of travel and driver rest times, and more.
“In the first few months, we determined that more than 50 hours each day were lost due to the microunavailabilities [small gaps in contractors’ work hours] identified. This is the equivalent of losing the use of more than two trucks per day,” said Fernandez Grossi. “Now, we obtain better information for the analysis of delays and easily identify optimization opportunities for the trucking fleet.”
This includes planning out downtime; making improvements to operations at production facilities, service stations, and carrier bases; optimizing loading and unloading processes; and better defining travel times. The system also supports implementing penalties for noncompliance, and it alerts PAE staff when drivers exceed their rest time or make unauthorized stops. In addition, it informs PAE staff when contracted trucks are available to make new deliveries.
One of the best benefits to PAE’s customers, according to Fernandez Grossi, is that the system sends them an estimated time of arrival for their deliveries using real-time traffic data alongside the OD Cost Matrix.
“We also send a WhatsApp message to the customer an hour before the arrival time,” Fernandez Grossi added.
In the future, PAE plans to extend the solution to its upstream operations and provide greater efficiency and cost-optimization for work order programming and monitoring.
“We would also like to promote ‘where’ as the foundational element in our business,” said Fernandez Grossi. “This will include integrating location in our other projects to develop synergy among them. We think that the ‘where’ is a key factor in the implementation of an effective digital transformation for the Pan American Energy Group.”