At San Diego State University in San Diego, California, the football team, called the Aztecs, plays the best of the best in Division I of the National Collegiate Athletic Association (NCAA) at Snapdragon Stadium, which opened at the start of the 2022 football season. For the university, the 35,000-seat outdoor college arena—which hosts football games, professional soccer matches, and other public events—offered an opportunity to engage in sustainable building practices.
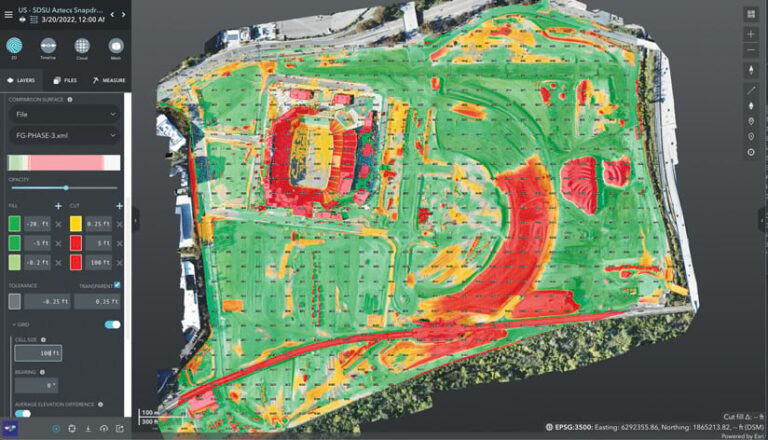
The construction of Snapdragon Stadium involved recycling all the concrete from the stadium that San Diego’s former professional football team, the Chargers, used to play in and redistributing it as the subbase material for the roads that service the university’s new stadium and 132-acre Mission Valley campus. This entailed processing more than a million cubic yards of materials from the demolished arena at an on-site batching plant and moving it to the adjacent construction site.
OCMI, Inc., a California-based firm that provides estimating, scheduling, and project and construction management services, oversees capital projects at the university. The firm needed a solution to help track the movement of materials around the construction site and provide progress reports to stakeholders.
“We needed a way to track and understand how those materials were being moved in conjunction with the schedule and be able to validate [the information that contractors] were giving us,” said Justin Dorsey, project executive and preconstruction manager for OCMI.
Dorsey and his team elected to use drones to fly around the project site, along with Site Scan for ArcGIS to collect, process, and analyze imagery. This would allow them to not only keep tabs on materials but also monitor construction and provide progress reports and metrics to stakeholders at the university.
This was a high-profile project for the community and part of a larger, multimillion-dollar construction venture, so Dorsey was determined to do the best job possible.
“[The old stadium] was a relic to San Diego residents. So that was quite a big deal that the stadium where so many memories were made was going away,” he said. “Knowing the gravity of that project…we had to knock it out of the park for the community.”
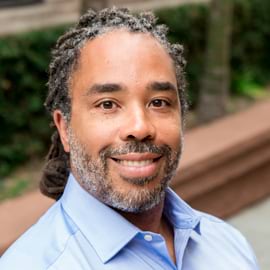
Site Scan fit the bill for what we were looking for, and it gave me the flexibility to scale. My goal is not for me only to fly but for me to grow [drone use] as a business line within my organization and run it from the enterprise level.
A Flexible, Scalable Drone Solution
In searching for the right software to use with drones, Dorsey found the scalability of cloud-based Site Scan to be a defining factor. He also liked the tools that came with it.
“Site Scan fit the bill for what we were looking for, and it gave me the flexibility to scale,” he said. “My goal is not for me only to fly but for me to grow [drone use] as a business line within my organization and run it from the enterprise level.”
Another benefit of using Site Scan was that it was “drone agnostic,” according to Dorsey. Other solutions he researched required users to purchase the drone along with ground control points and other proprietary hardware, which would lock OCMI into using one company’s products. Site Scan, however, is compatible with a range of drone technology. Recently, when one of his organization’s drones required maintenance, Dorsey was able to continue flying weekly missions using his personal drone.
Dorsey was also able to learn how to use Site Scan quickly and easily because it is user-friendly and intuitive. After receiving airspace authorization at the project site, Dorsey began flying his drone every Thursday to take images of the construction.
“I went out, and I took my drone out and flew it, and I tried to reverse engineer how I thought the software would work,” Dorsey said. “The datasets were pretty large—about 700 to 900 photos per mission.”
For the stadium construction project, which began in 2020, Dorsey said his typical workflow was to fly over the site with a drone, upload the images to Site Scan, and then process the imagery. He shared a weekly distribution report with stakeholders that showed the site plan and included a link to a 2D orthomosaic and a 3D mesh model that let users walk around the site remotely. Dorsey also included videos from his flights.
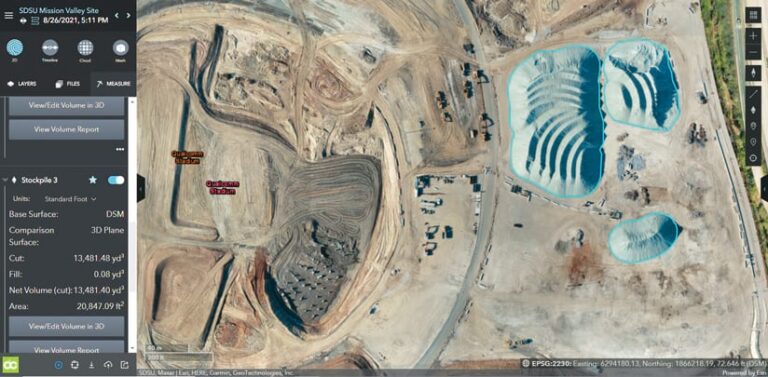
Capturing the Right Metrics
Because site construction began at the height of the COVID-19 pandemic, using Site Scan was key for Dorsey and his team to keep stakeholders up-to-date on the project.
“I [would] get requests from clients [that said], ‘Hey, can I get that new plan? […] It created a sense of awareness of [the] project site from a visual aspect,” Dorsey said. “People do like the 3D mesh model. That does give them visibility on the project site.”
Dorsey was pleased that Site Scan gave him the ability to create models. He and his team recently used the software to complete a topographic survey of the new women’s lacrosse field at San Diego State University. Using ground control points of the field, he said he completed a drone flight in 15–20 minutes and was able to immediately process the data to create the survey. Getting a plane or helicopter to fly the same mission could cost $8,000 to $10,000, so the use of a drone and Site Scan led to significant cost savings.
“Back when I was flying a drone as a photographer, I was just taking artistic photos or getting to spots that I wanted to capture. But you couldn’t create models,” Dorsey said. “So I see the value of how this is going to start to weed out some of those big-dollar costs on projects if you have the right tools in place to do so.”
On the Snapdragon Stadium construction project, using Site Scan enabled OCMI team members to obtain the metrics they needed for their client. When the original stadium was being taken down, construction personnel created large stockpiles of concrete, and an on-site batching plant was set up to reprocess it. OCMI was asked to get quantity takeoffs on the stockpiles—that is, to estimate materials—and Dorsey and his team were able to use Site Scan to run volume calculations that told grading subcontractors exactly how much material was excavated.
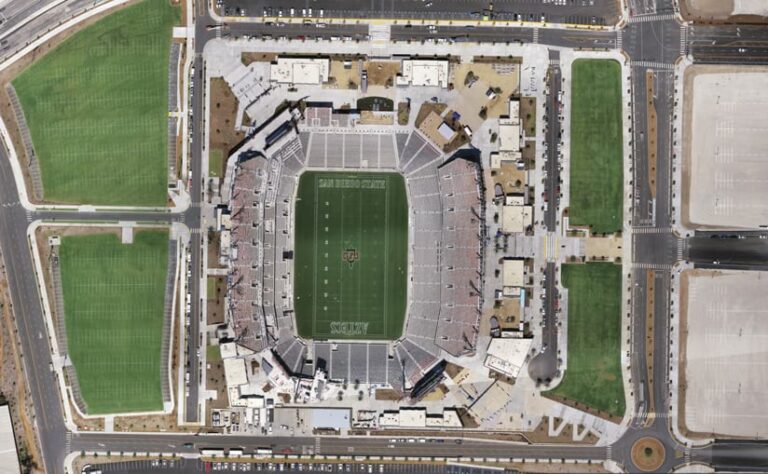
“When we were faced with a change order request, we were able to quantify exactly how much material was in the various three stockpiles on-site, which then we were able to [use to] thwart the claim that there wasn’t enough material to fulfill the base [of the stadium],” Dorsey said. “So that was a big win for having [Site Scan].”
Knowledge Sharing for Continued Returns
Despite the challenges of constructing a new stadium with recycled materials during a global pandemic, Snapdragon Stadium was built on time and came in under budget.
The successful deployment of Site Scan for the stadium project has led Dorsey and the OCMI team to use it for other construction projects as well. And Dorsey’s end goal is to pass on the knowledge he’s gained and teach other pilots how to employ the technology.
“I’m thinking, how do I scale it?” Dorsey mused. “It’s just something that I’m really passionate about and want to invest in. I think there are a lot of returns when it comes to where [Site Scan] is going.”