GIS Reduces Complex Construction Supply Chain Challenges
Construction projects require solving complex supply chain management (SCM) challenges — an area where GIS has proven to be an excellent solution. Virtually every industry already uses Esri’s ArcGIS to manage the meta and micro level details of SCM. The world’s largest logistics and shipping companies couldn’t operate without ArcGIS powerful data collection and location analytics; retailers and restaurants around the globe and around the corner are kept stocked and ready to open their doors with GIS-based analysis; utility companies plan for growth and respond to outages by dispatching people, equipment and materials based on location of the lines, population areas effected, and proximity to operational equipment.
However, construction is unique compared to many other industries – the nature of the project typically being a one-off situation, where teams (and teams of teams) are brought together to work collaboratively on a single deliverable. And, AEC projects are complex due to the need to specify and track hundreds (if not thousands) of materials, dozens (if not hundreds) of companies, expensive tools and equipment, and to coordinate potentially thousands (if not tens of thousands) of construction activities.
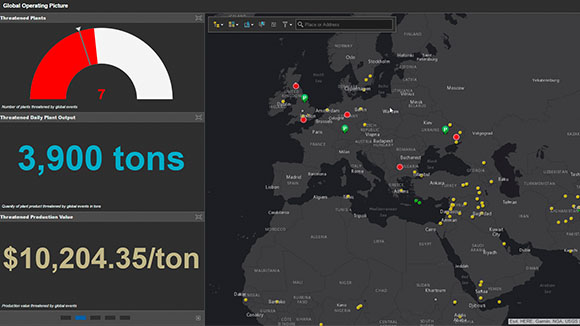
BIM authoring tools have been attempted to monitor construction activities and manage construction supply chains. However, because sourcing, warehousing, and deliveries often occur beyond the actual construction project sites, BIM fails to meet the needs of construction supply chain management. The purpose of most BIM solutions, whether authoring, visualization or estimating, are not easily extended to the challenges of logistics management. Modeling solutions and model-views may be perfect representations for many AEC workflows; however, GIS is well suited to address supply-chain-management challenges.
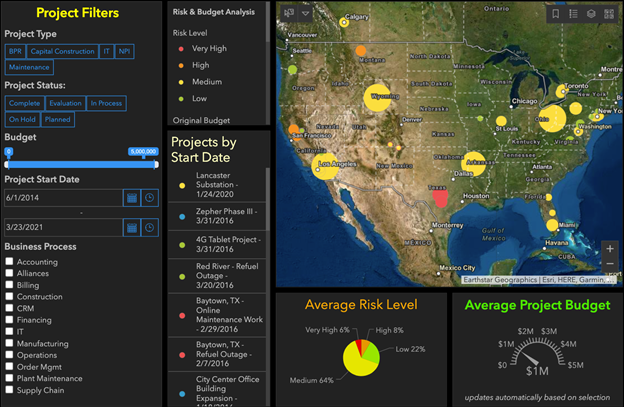
AEC project supply chain management requires:
Inventory management: Project planners expect to know the availability of commodities, made-to-order items, and raw materials for their project, as well as insights into the timing and location when that expectation is not met. Planners overseeing projects of substantial size, scope and timeframe need to forecast the inflow and outflow of inventory as part of their look ahead and master planning.
Warehouse oversight: Projects occurring across a large geography or for companies working on a portfolio of projects, material distribution centers, or warehousing is common. When practice is in place, managers oversee all activities taking place in the warehouse, and they analyze aspects such as storage which may occur under the roof of a building or may be located at one or more lay-down areas of a construction site – locations that change and move as the project evolves towards completion.
Fabrication tracking: This involves handling the arrival of raw materials, processed into sub-assemblies or modules, and delivery of the final product. As the industry shifts toward modular construction, design for manufacturing and assembly (DFMA) grows in adoption, and fabricators drive their machinery from BIM data, the need for tracking fabrication will increase.
Sourcing and supplier management: Effective project delivery requires identifying viable suppliers using several criteria, including location. Distance from the factory to jobsite impacts LEED and other sustainability goals, and the location may impact the quality and cost of raw materials and finished products. The ability to mobilize teams of people, job sites, materials, equipment, tools can determine whether a project is delivered on time and within budget.
Analytics: Intelligence to analyze the wide range of planning, scheduling, coordinating and communication problems and find their causes as well as provide suggestions for reducing risks.
GIS uniquely coordinates and helps manage many elements of AEC, including the supply chain chaos of built projects. By linking the parties and their locations in the construction project – utilizing locations of the project, staff, supplier sites, raw goods, and material warehouses – GIS can be an essential tool for AEC project supply chain management.
.
Improve Reality Capture with GIS
Since the earliest days, GIS has allowed AEC professionals to map and model their projects as a virtual representation of the project-sized portion of the real world. Raster and vector data have been combined with various data sources to create layers of features giving a virtual view of the real world.
Combining these GIS models with drone and aerial imagery, point clouds, and 3D mesh in an engaging environment is the next step in a class of applications that solve AEC challenges.
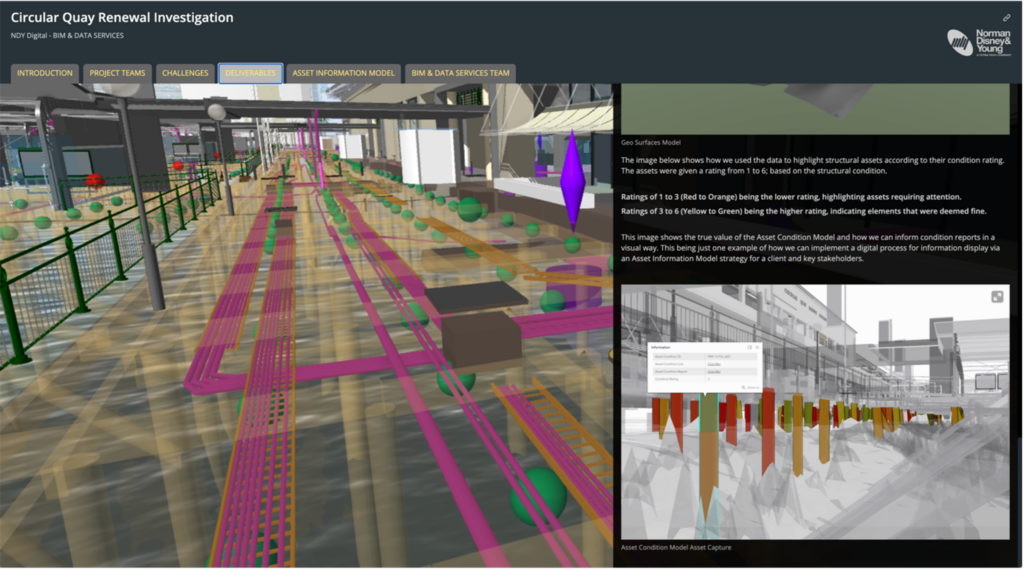
The ease of scanning allows one person to go onsite to capture more information which is more usable in a few hours than a team of people would do in days or even weeks. And, scanning captures every detail which can be shared with all the stakeholders of the projects leveraging the combined talent of the team.
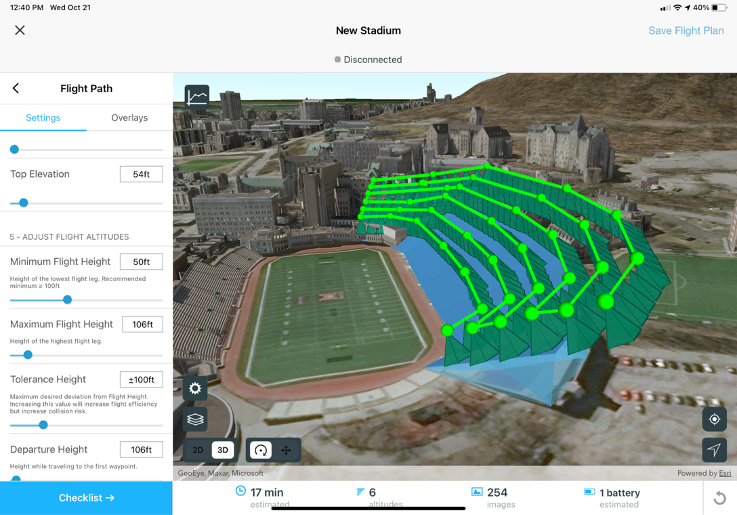
The volume of sensors and mobile devices producing massive amounts of data has been exploding over the past few years. As the use of digital twins grows and the amount of data we are now collecting increases the fundamental workflows of reality capture will continue playing a major part in construction project delivery. The role of GIS and location intelligence in managing these datasets is vital – it becomes the glue to connect and integrate them.
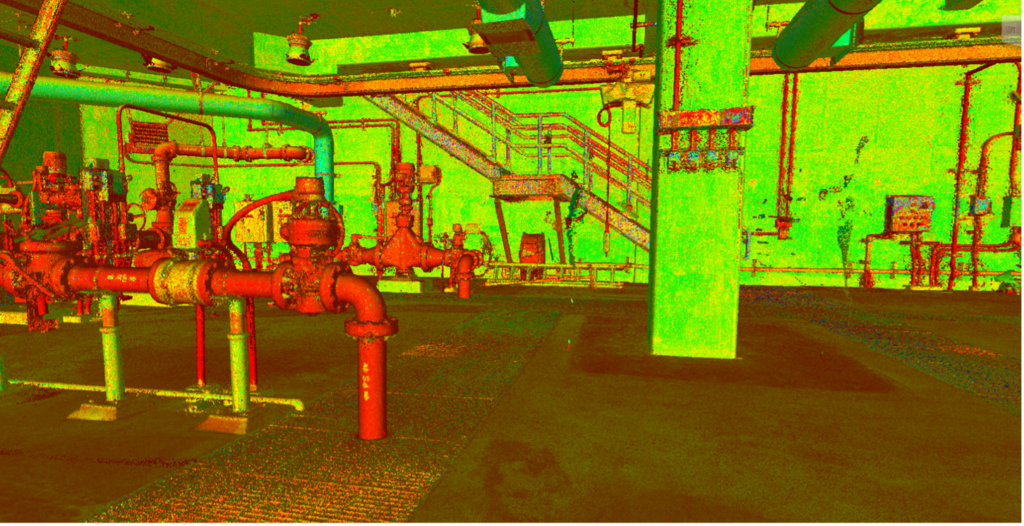
ArcGIS provides reality capture and photogrammetry software that transforms drone, aerial, satellite, and historical images into authoritative 2D and 3D views of a project at critical times.
Using these layers of imagery, AEC professionals involved in all project phases can create real-world depictions of large construction sites, cityscapes, and entire regions. Teams become capable of assessing infrastructure, detecting change, monitoring the environment, and more.
Interested in learning more – Fill out this contact form and an Esri expert will reach out to schedule a meeting.