For seasoned veterans in the infrastructure realm, the most impressive thing being built today isn’t a bridge or a skyscraper—it’s a digital version of the worksite itself.
In construction zones across the globe, trucks rumble in with their payloads, cranes orchestrate the movement of huge steel beams across urban skylines, and excavators haul massive buckets of dirt. What’s new is the ability of construction innovators to use digital twins to monitor and even predict what’s happening on the ground.
Executives can monitor progress with lifelike digital models thanks to drone imagery. Sensors tracked by geographic information system (GIS) dashboards reveal supply chain disruptions in real time, allowing managers to respond. With the rise of modular integrated construction (MiC), planners are using software to visualize installation sequences and sync just-in-time (JIT) deliveries, leading to a seamless building process.
“We talk about having to change your mindset from a traditional construction company to a logistics-based or manufacturing-based approach,” says Paul Evans, an executive director and CTO at Gammon, one of Hong Kong’s most innovative construction and engineering firms. “And to do that you need new tools.”
With leading GIS technology, construction professionals create digital twins, integrating data and systems into virtual representations of assets. Paired with building information modeling (BIM) software, location technology can represent not just the structure itself, but the environment around it, creating operational awareness of shipping routes, environmental impacts, or weather patterns. With that level of intelligence, leaders can plan more efficiently, reducing waste and costs while anticipating and mitigating worksite hazards.
In the world of Hong Kong construction, Gammon is a digital twin pioneer, deploying a proprietary model called GTwin on projects ranging from the Lyric Theatre Complex, a 1,450-seat performance space, to the business park Cyberport. As Gammon’s digital twin model has evolved, the role of location analytics has broadened to several areas, from informing site planning to creating alerts that help prevent on-site collisions.
“Over a period of one or two years, the GIS component really starts to embed with the broader business things you’re doing,” says Evans. That, in turn, gives Gammon a competitive edge in a bustling market.
How Digital Twins Expand Operational Awareness
Architecture, engineering, and construction (AEC) businesses are adopting GIS-based digital twins for many reasons. They’ve been employed to enable 5D project management, guide 20-year infrastructure plans for corporate campuses, and create greater transparency between owners and clients. Digital twins are prized for their ability to facilitate data management and sharing, as well as project reporting.
In Hong Kong, government leaders and the Construction Industry Council (CIC) have encouraged AEC firms to adopt digital twins to improve safety and project reporting—a call which Gammon was quick to answer. “Gammon always tries to step to the forefront of the industry,” says Dr. Stewart Wan, head of innovation at Gammon and leader of the company’s digital twin development team.
Gammon built its digital twins with GIS technology in part because the location software proved so adept at logistics planning—a priority for MiC projects (watch the video below). In modular construction, prefabricated parts of buildings are assembled elsewhere and installed on-site. Managing off-site logistics for those modules is key to keeping projects on schedule. An aging labor force and the high cost of materials have accelerated the embrace of modular construction.
GIS gave Gammon’s managers a 3D model of the city, the surrounding road network, and the building under construction. With this digital twin, they could optimize route planning to ensure that trailers arriving from different sites across the water in mainland China could convene on the site at the appropriate times. Such efficiency also aided Gammon’s efforts to reduce vehicle emissions.
“With GIS, you can link to real-time data from the road network,” Evans says. “You can even get alerts if there’s traffic jams and other incidents.”
Spatial awareness is crucial on the bustling streets of Hong Kong. With GIS-enabled logistics management, planners can avoid traffic blockages by bringing trailers into designated holding areas and sending them to the site on a JIT basis.
Geofencing also helps keep deliveries of modules on track. The routes of various drivers are programmed into GIS. If for some reason they stray from those paths, the technology automatically alerts both the driver and supervisor.
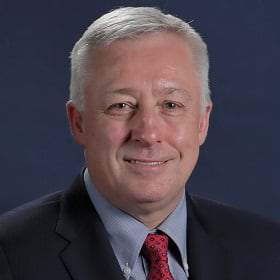
What we’re seeing now is more and more applications of GIS coming into the construction industry.
Gaining New Perspectives on the Building Design Life Cycle
Gammon’s early digital twins expanded operational awareness beyond the worksite to the roads and cityscape around it. As Wan, Evans, and the digital twin team envisioned new applications for the technology, they realized they could push the boundaries even further. For instance, by linking the digital twin dashboard to CCTV cameras in the mainland factories where modules are assembled, they could monitor the end-to-end manufacturing process.
On-site, GIS and BIM enabled a manager to juxtapose a 3D floor model of a modular project with the installation schedule. By analyzing the movements of workers and machinery via a smart map, they could increase safety and use space more efficiently.
Gammon’s leaders came to prize the GIS-based digital twin as a central interface for planning and design. On a single dashboard, they could distill data from drones, sensors, cameras, and other technologies. “It’s about the full life cycle of the building development,” Wan explains.
As GTwin technology has evolved, new applications have emerged. Managers can quickly analyze and measure the dimensions of a worksite in a digital twin. Armed with this location intelligence, Gammon’s leaders can save costs by optimizing equipment sizing and better predicting how long they will need rented equipment.
Sensor data tracked with GIS enables proximity detection, reducing the risk of collisions between equipment operators and employees on foot.
GIS is also aiding with reality progress capture, which involves gathering imagery of the building process with drones or lidar so executives can examine the span of construction stages in detail. “You’ll actually understand better how your project has been built—not how you think it’s been built—because you’ll have the data to tell you what physically happened,” Evans says.
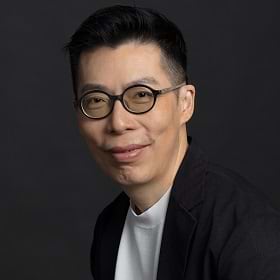
GTwin is a platform starting from the planning, design, during construction, and also leading to the operation.
Transformational Technology Meets an Industry in Flux
In Hong Kong, where the ferment of innovation produces many new technologies, decision-makers like Evans are frequently exposed to fresh ideas and cutting-edge solutions. But for Gammon’s CTO, a technology is ultimately only as good as the problem it solves. “There’s so many things out there you could do, and it would look really good on a PowerPoint or live demo, but where’s the real value coming out of it based on the investment?” he says.
For Evans and Wan, GIS-based digital twins address real pain points in the construction process, helping Gammon’s teams adapt and find new competitive edges in the quickly changing AEC industry.
“You’ve got to really get at the value proposition,” Evans says. “We certainly got that with the GIS technology that we overlaid on the plant and equipment and vehicles, and certainly we got that with the tracking of the logistics out of the factory.”